Manufacturing
Reducing unscheduled downtime and maximizing productivity
Pain points in your industry: why you need a CMMS
Maintenance management can literally make or break a manufacturing company. Think about it. Manufacturers rely on high-value assets to produce consistent output to meet demand. Their profit margins are contingent upon achieving the highest possible return on investment (ROI) from their assets by keeping them in optimal working conditions and producing the highest possible yield— all while controlling maintenance costs.
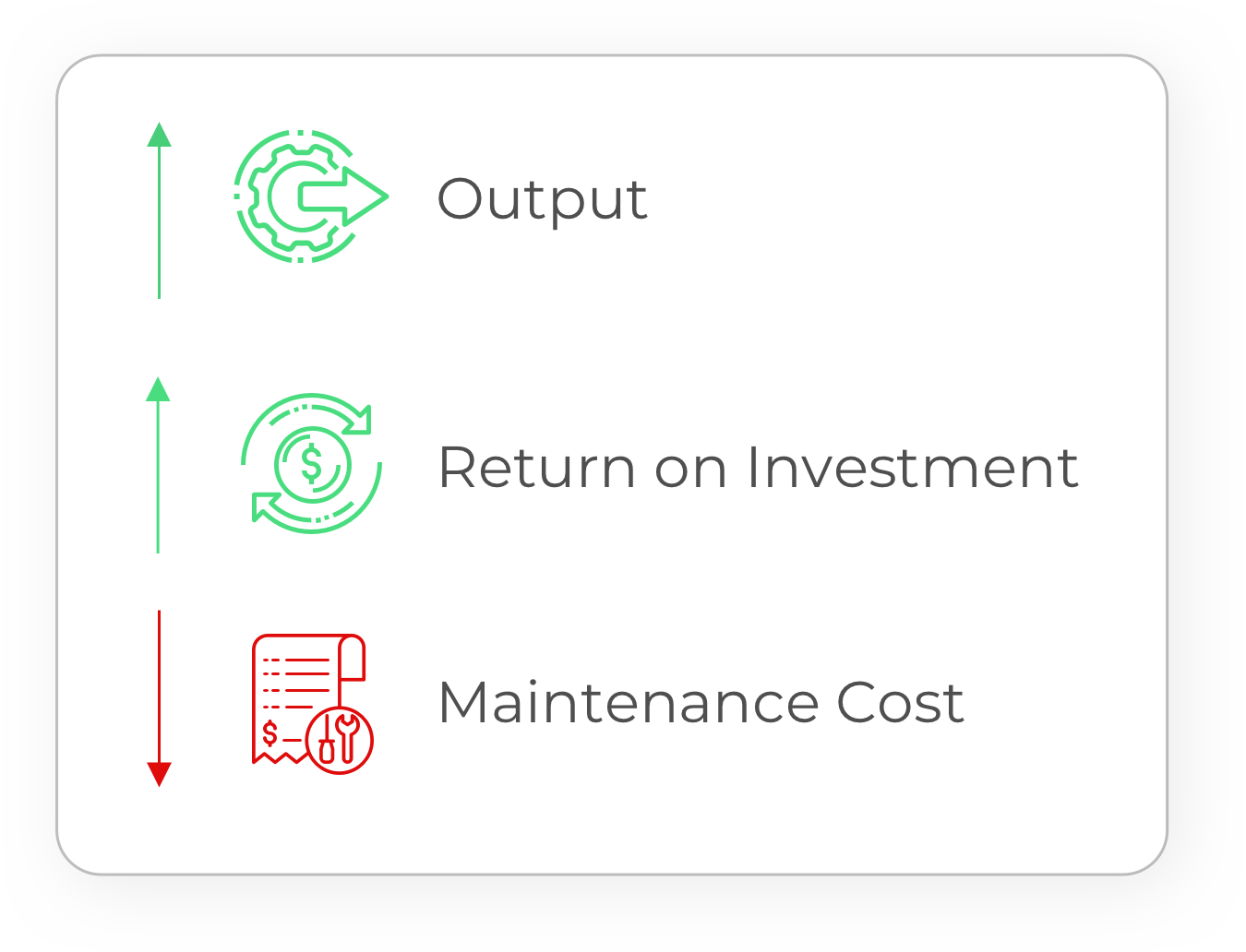
Unplanned downtime caused by poorly maintained equipment can be financially ruinous. According to analyst firm Aberdeen: “The cost of unplanned downtime can be devastating, ranging from an estimated $10,000 to $260,000 per hour for industrial plants.”
Manufacturing companies face a number of pain points that make it hard to comply with regulations, keep costs down, and remain competitive.
- Materials shortage — Supply chain disruptions can lead to materials shortages for small- and medium-sized manufacturers. A CMMS enables you to use just-in-time inventory management, which frees up warehouse space and ensures technicians have the right parts on hand to perform necessary maintenance.
- Manufacturing downtime is expensive — Research from Arimo shows that manufacturers have to deal with up to 800 hours of downtime annually. Studies show that almost every factory loses at least 5% of its productive capacity to downtime, and many lose up to 20%. Lost production time directly impacts the business’ bottom line and reduces profits.
- Labor shortage — Optimizing wrench-on time leads to a more engaged workforce, while a mobile-first CMMS enables technicians to receive work orders from anywhere. Manufacturing plants that implement strategies like Total Productive Maintenance (TPM) empower employees to assume an ownership mentality over their work and the equipment they use.
- Backlog of orders — The backlog for manufactured goods currently stands at $1.23 trillion, according to Axios. Without a change to their business model, smaller manufacturers will struggle to keep pace with demand. A CMMS enables you to spot inefficiencies and keep equipment in good condition, leading to greater yield and fewer backlogs.
- Missing information —Manufacturing companies must share information across the entire value chain. For example, technicians need the right work instructions for the task at hand. Executives need access to data to make business decisions. Supply chain partners need real-time information on output and logistics. A CMMS helps coordinate information-sharing between different parties by providing real-time analytics and an in-app chat function while enabling technicians to work remotely.
Protect your most critical assets and facilities
The main purpose of a CMMS is to extend the life of your organization’s most critical assets using a preventive maintenance plan. Here are some of the most important assets in a correctional facility. A CMMS helps you manage your inventory and keep track of asset information such as purchase date, number of work orders, details of work done, and so on.
Critical and auxiliary assets | Critical sites |
|
|
How can a CMMS help?
For manufacturing companies, a CMMS is critical to remaining competitive in today’s economy and complying with regulatory standards. Modern maintenance management software enables you to address potential bottlenecks efficiently. By providing you with real-time maintenance operations data and automating key processes (eg: work order scheduling, service requests, preventive maintenance tasks, analytics), a CMMS mitigates production obstacles.
Meet production goals
Whether you are manufacturing a continuous product or separate units, in one plant or in multiple plants around the world, you can use MicroMain’s CMMS to:
- Maximize plant output
- Minimize equipment downtime and waste
- Prevent labor overtime
- Reduce needed inventory
- Optimize preventive maintenance to keep equipment working at full capacity
Meet plant-specific needs
MicroMain software includes comprehensive features related to automated work orders, preventive maintenance scheduling, asset tracking, inventory and cost control. In addition, you have many customization and add-on options:
- Collect data used for workflow decision making in PLM
- Track costs related to PLC or CNC maintenance
- Contribute to Six Sigma quality initiatives
- Access Material Safety Data Sheets, including attachments to work orders
- Follow procedures related to PLM such as minimizing scrap through inventory/parts re-use
- Provide data showing compliance required by OSHA, FDA, EPA and other agencies
Benefits of having a CMMS
Using a CMMS helps you reduce unscheduled downtime, manage your maintenance costs, and gain data insights into your maintenance operations so you can keep optimizing.
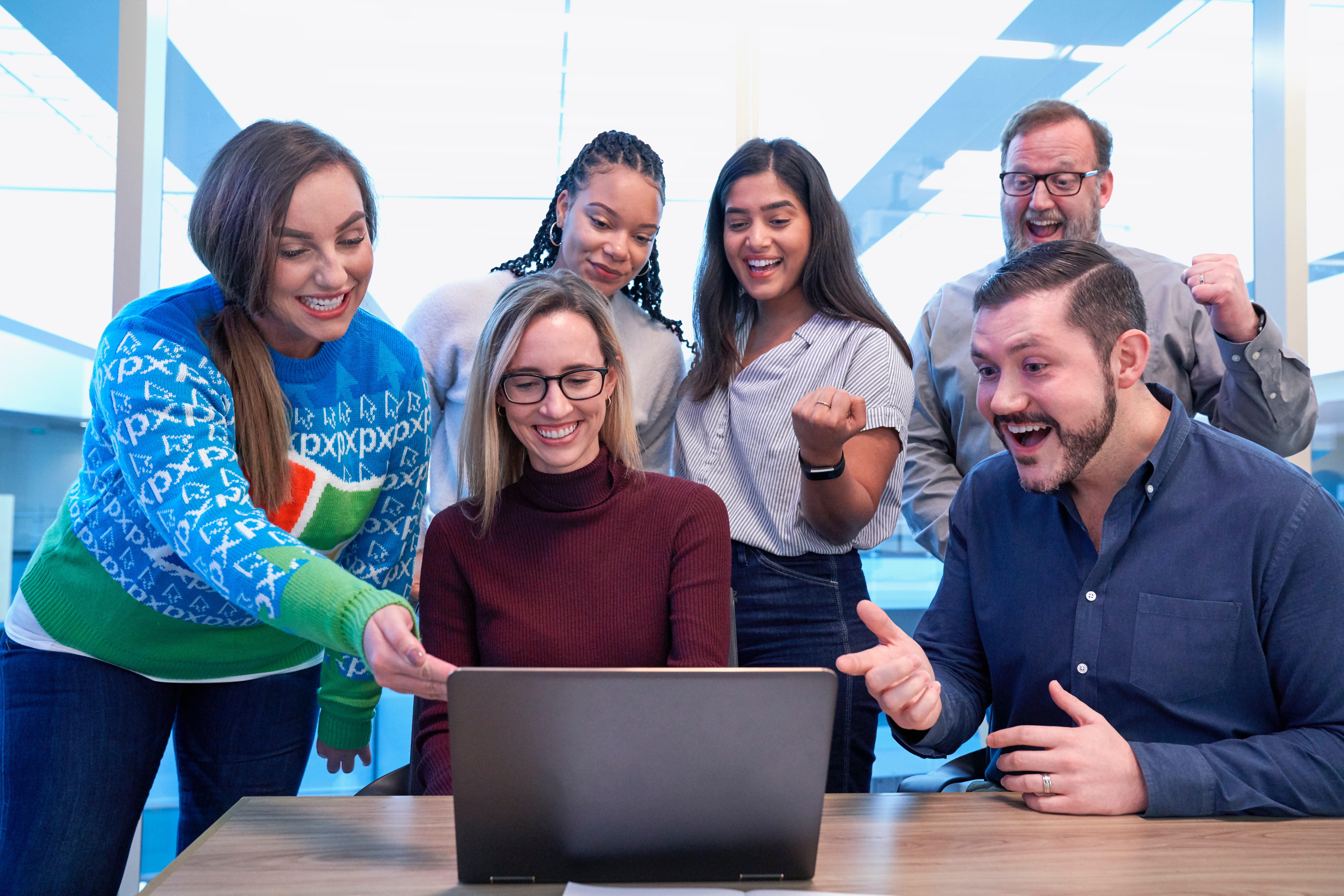
Maximize equipment uptime
To maintain equipment availability, you must respond quickly to requests for emergency repairs. With MicroMain software, you can identify the right labor and parts and immediately issue work orders detailing the repair needed.
You can use the software to store data or integrate it with other tools to enable proper procedures for repairing equipment on the plant floor. These procedures may be required according to internal company policy or even federal regulations.
Forecast budgets accurately
Detailed cost and time analysis reports, including total cost of ownership (TCO) for assets and parts, will give you the granular data you need to accurately project budgets.
These reports will help you evaluate productivity and make adjustments to improve labor utilization. In addition, you can show extended asset lifespan using preventive maintenance, thereby reducing emergency purchases and overtime costs.
Organize data and operations
In some manufacturing companies, different plants are responsible for different products in the manufacturing process. Some companies even organize maintenance needs by department, floor, or area.
On top of that, facilities, grounds, parking garages, and plant-related support systems must be maintained. Maintenance management software enables you to segment your data any way you like, so you can measure costs and productivity on a plant-wide and enterprise-wide basis.
Generate reports to communicate data insights across the company
With MicroMain software, you can run top-level reports for supervisors or CFOs. For your own department, you can access multiple, detailed reports to help you fine-tune your maintenance management operations. MicroMain includes more than 400 standard reports concerning assets, labor, parts, costs, and more.
Make cost-effective business decisions
MicroMain gives you the tools you need to control labor, contracted services, parts, and asset maintenance costs. From pressure regulators to metal fabrication systems, you can use historical, current, and projected costs to better manage dollars spent on equipment maintenance.
Brands we work with
Here are a few brands in the maintenance industry that trust Micromain to support their maintenance operations.
.
Manufacturing Client Testimonial
“Before we had MicroMain’s software, we lacked a lot of the information necessary to make informed decisions. Now we input the data, develop reports and track our trends so that we can make better decisions. The investment was reasonable and the payoff has been unbelievable.”
Jeff Nevenhoven
Other ways a CMMS can help manufacturers optimize maintenance management
1. Streamline the reporting process
A CMMS provides a fast and easy way for machine operators and other employees on the shop floor to report problems. A work order request portal allows anyone to submit work orders, while enabling maintenance teams to maintain a digital trail, prioritize work orders, and facilitate scheduling.
You can customize the work order request form by allowing users to submit photos and indicate priority level plus other information such as building number (in a large facility) and equipment type. Detailed work orders enable technicians to complete maintenance tasks without delays while minimizing error.
2. Optimize the workflow
Create a set of standard operating procedures technicians can use to maintain complex assets. A preventive maintenance strategy minimizes the chance of unscheduled downtime by performing maintenance before an asset shows signs of wear. However, not all assets should be placed on a preventive maintenance plan. Routine inspections and corrective maintenance help you circumvent machine failure for medium-value assets that don’t warrant the high upfront investment of preventive maintenance.
CMMS features facilitate this process by providing the following:
- Detailed maintenance logs for every asset
- Spare parts management stem (so you never run out of replacement parts)
- Documentation for each asset (OEM recommendations, fault patterns, and maintenance procedures)
3. Manage work order scheduling
Automated work order scheduling means work orders are assigned according to priority level and technician availability. Recurring work orders—eg: routine inspections or preventive maintenance tasks—are automatically scheduled so you never miss one.
When a new work request comes in, the maintenance planner sees a real-time view of what each technician is working on and which ones can be safely pulled into other tasks. It’s always best to use a technician who isn’t in the middle of another task instead of interrupting a task that is in progress.
A CMMS gives you insight into the following:
- List of active maintenance tasks
- List of tasks that still need to be scheduled
- Which technicians are assigned to cover which tasks
- Who is available to cover corrective tasks that still need to be scheduled
4. Create communication channels
Remember that maintenance doesn’t only concern the maintenance team. Employees who work with assets that are waiting to be repaired need to be updated on the progress of maintenance work. A mobile CMMS comes with a built-in chat function that makes it easy for managers to communicate with each other on-site, as well as push notifications that notify managers of important changes.
Conclusion
Manufacturing companies are increasingly competing on factors like the customer experience and the ability to meet demand, which leaves no room for error. A CMMS enables manufacturers to maximize the ROI of their most high-value assets, reduce unscheduled downtime, and maintain the highest level of productivity with available resources.
Preventive maintenance helps organizations avoid costly downtime and unsafe working conditions while lengthening the useful life of assets. However, an effective maintenance strategy should also include corrective and reactive maintenance for non-critical assets, and there is no easier way of implementing the right maintenance strategies than with a CMMS.
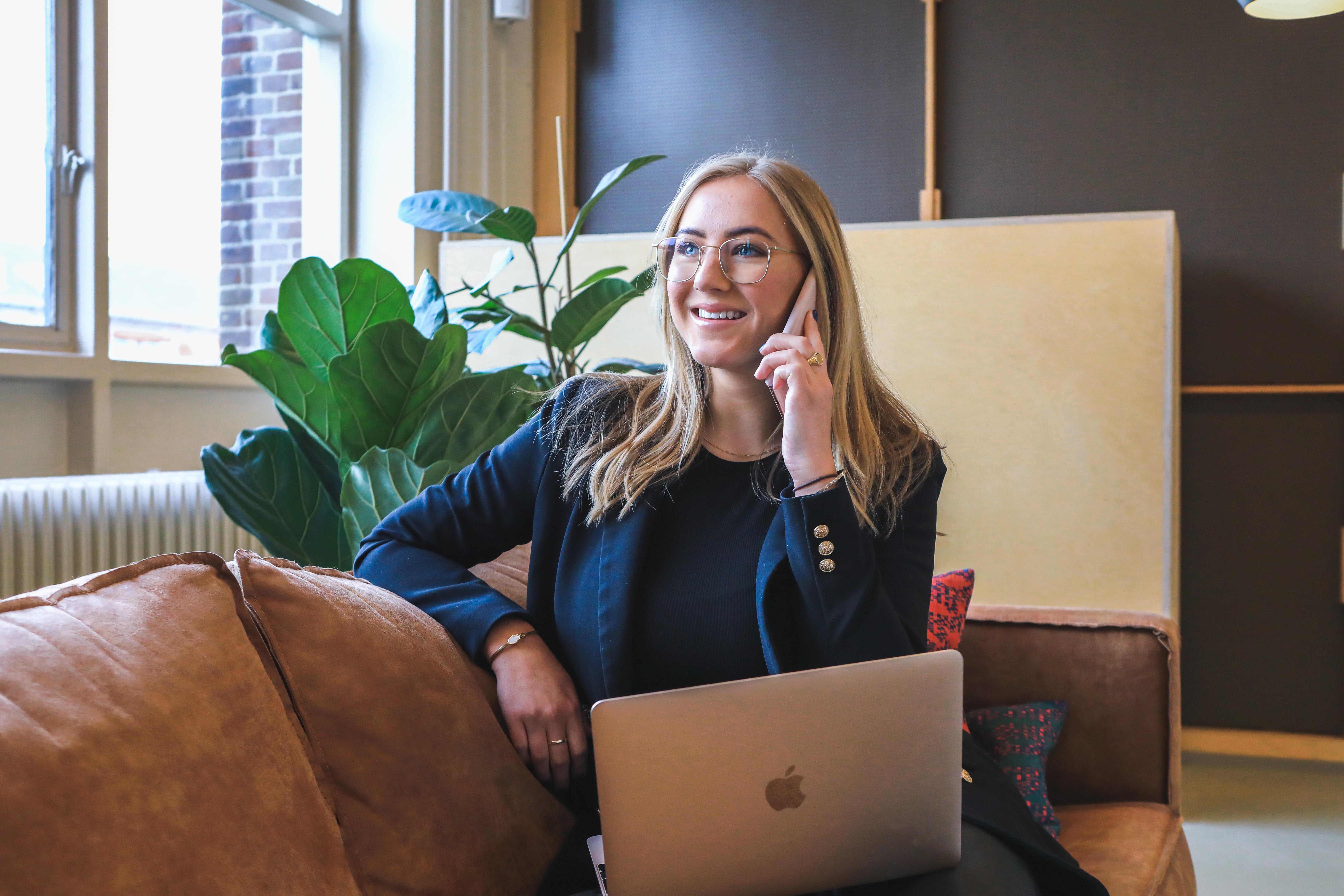