Building Maintenance
Keeping residential and commercial properties safe and livable.
What is building maintenance management?
Without proper maintenance, buildings become unsafe and unlivable. Building maintenance refers to activities performed to keep residential and commercial properties in a safe, functional, and comfortable condition. This includes tasks such as cleaning, landscaping, and electrical system maintenance.
Much of property maintenance management consists of behind-the-scenes work: for example, removing trash, replacing light bulbs, and cleaning common areas. Building maintenance management is a process for controlling maintenance resources and activities required to preserve, repair, or replace assets within a residential or commercial facility.
When it comes to residential properties such as apartment buildings, maintenance management also consists of fulfilling work order requests from tenants, preparing vacant units for occupancy, water-proofing the building, and updating electrical appliances.
Who is in charge of building maintenance?
Building maintenance tasks are carried out by a team of professionals, each one with a specific function:
Janitors - Custodians are responsible for maintaining the cleanliness of a built environment. They mop floors, vacuum carpets, clean bathrooms, wash windows, and more.
Maintenance technicians - Technicians perform the maintenance, inspections, and repair of building systems including HVAC, electrical, and water systems. These tasks are typically assigned by work orders.
Maintenance supervisors - Supervisors plan, assign and manage a team of maintenance workers based on incoming work order requests. When assigning work orders, they take into consideration the existing maintenance backlog as well as the maintenance department’s short- and long-term objectives. They then prioritize the maintenance department’s work for the day or week.
Maintenance planners - Maintenance planners are responsible for coordinating all plannable maintenance work on their premises. These professionals are usually found at large manufacturing facilities but may be in charge of building maintenance as well.
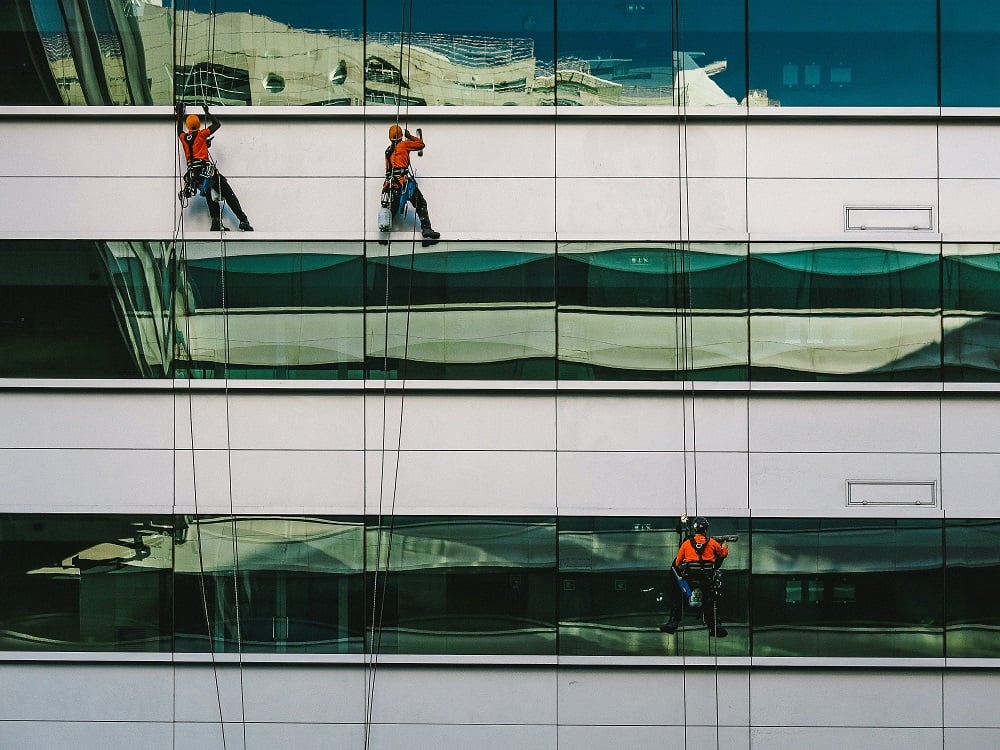
Here's why building maintenance is important
1. Safety
A poorly maintained building is a safety hazard. Corrosion from the elements, wear and tear from use are just a few reasons why electrical and structural systems will all need maintenance, repair, and/or replacement eventually. Cutting costs or treating maintenance as an afterthought can create a hazardous situation for your employees or tenants.
2. Saving money
Keeping up with maintenance projects is much less expensive than executing an emergency repair. Budgeting for regular upkeep is much easier than having to spend a large amount all at once in the event of an emergency. Here are some strategies for saving money on building maintenance:
Schedule preventive maintenance
Preventive maintenance is a type of scheduled maintenance that is performed regularly on a piece of equipment regardless of whether or not it has failed. This is done to prevent unexpected equipment malfunctions or emergency situations that may endanger people’s lives or interrupt business-as-usual. For some organizations, preventive maintenance constitutes 90% of all maintenance activities.
Maximize the building's energy efficiency
Commercial buildings require a lot of energy to heat and cool. If the building is not optimized for energy efficiency, consider retrofitting windows, HVAC systems, ventilation systems, and roofing that is designed for better insulation. However, making a building more energy-efficient doesn’t always require a huge investment. Routine maintenance tasks such as cleaning air ducts, changing air filters regularly, and using sealant to prevent HVAC leaks reduce overall energy consumption.
You can also economize on the building’s energy use with low-budget fixes such as replacing tungsten light bulbs with LEDs, choosing better window treatments, and using Energy Star-rated appliances.
Use a CMMS to track asset lifecycle
Tracking asset lifecycle is the only way to determine if your current maintenance plan is working. Pay attention to failure metrics including Mean Time To Failure (MTTF) and Mean Time To Repair (MTTR) as these indicate whether your assets are being over- or under-maintained.
5. Functionality
Routine maintenance is essential to building functionality—taps that run when you switch them on, a roof that doesn’t leak, and an HVAC system that supplies the building with cool air during the summer months.
6. Compliance
The International Property Maintenance Code (IPMC) establishes the minimum requirements for the maintenance of existing buildings. Building managers have to keep up with the maintenance of all systems per code and regulatory requirements including the WCB Occupational Health and Safety Regulations.
Examples of building maintenance
1. Cleaning common areas, trash removal, replacing lightbulbs, pest control, appliance repair
2. Weatherproofing the building ahead of a major weather event or removing snow
3. Maintaining electrical, plumbing, and HVAC systems to ensure climate control and electricity/water access
4. Outdoor property maintenance including landscaping, lawn care, and sprinkler management
5. Checking and replacing fire extinguishers, smoke detectors, etc.
6. Maintaining an aesthetically pleasing environment— eg: painting fences, trimming hedges, removing litter
What are the benefits of building maintenance software?
Building maintenance software, also known as facility maintenance software, is a tool that helps building managers oversee the upkeep, repair, and maintenance of their premises.
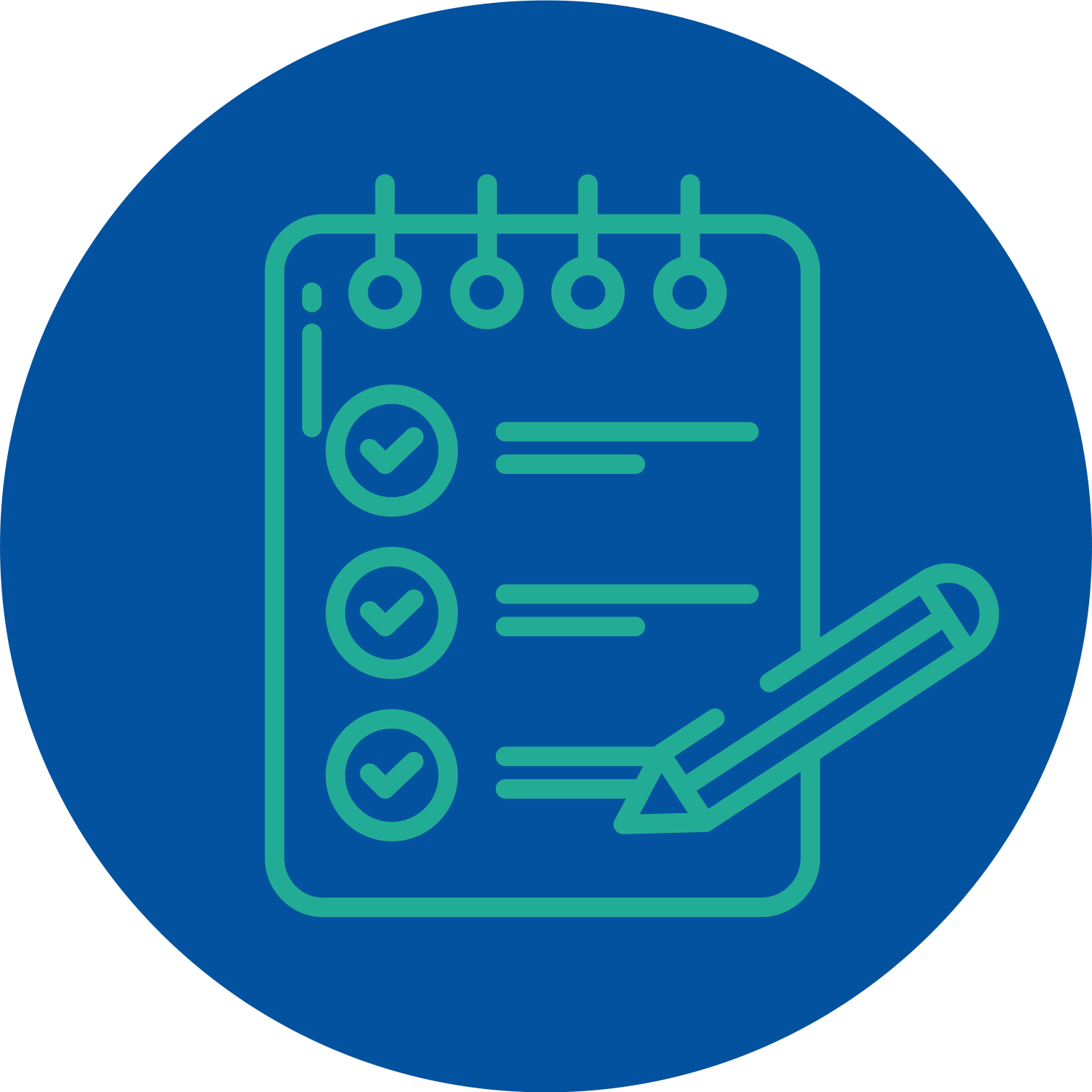
Assign and track work orders in real-time

Plan preventive maintenance and automatically generate recurring work orders
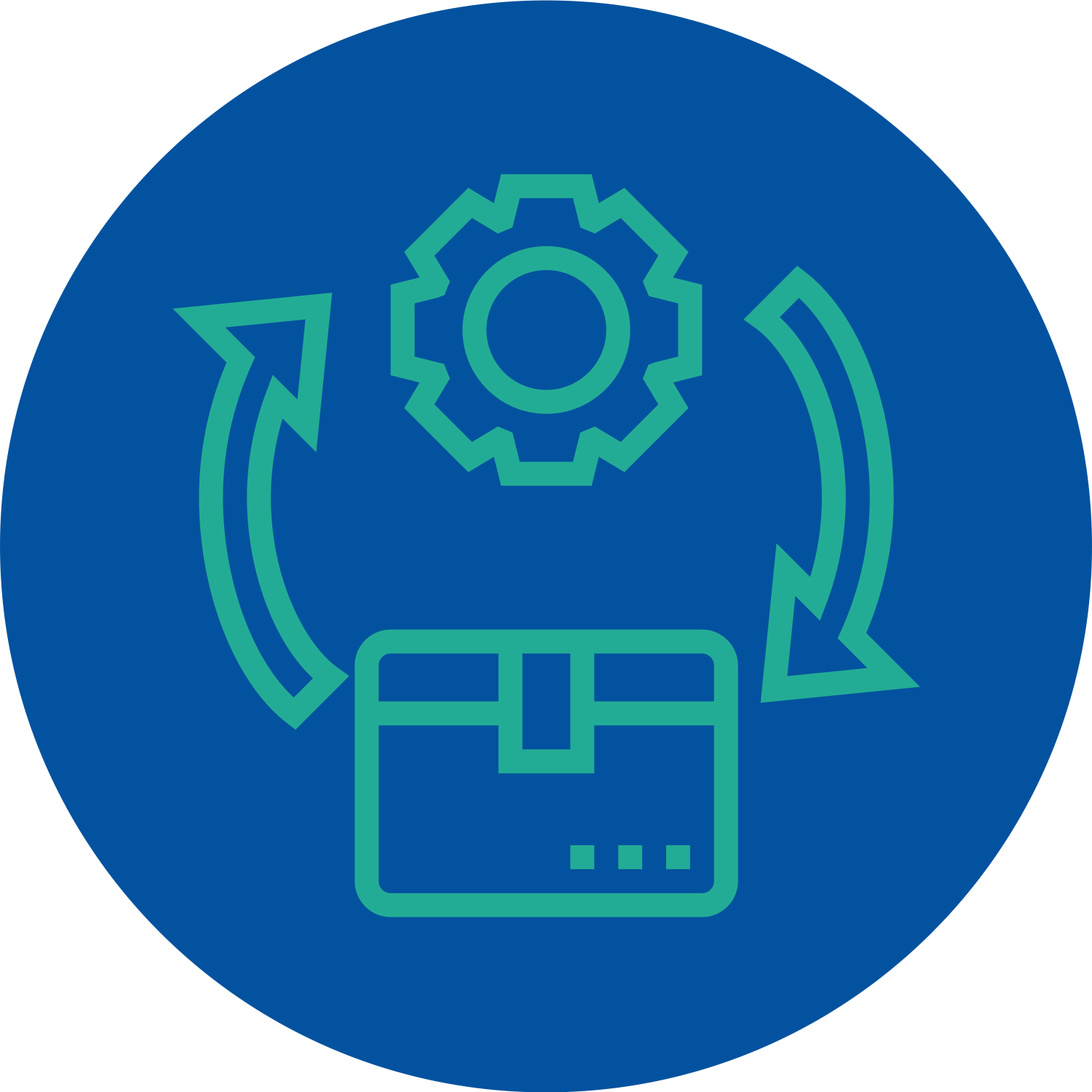
Measure and track asset life cycle
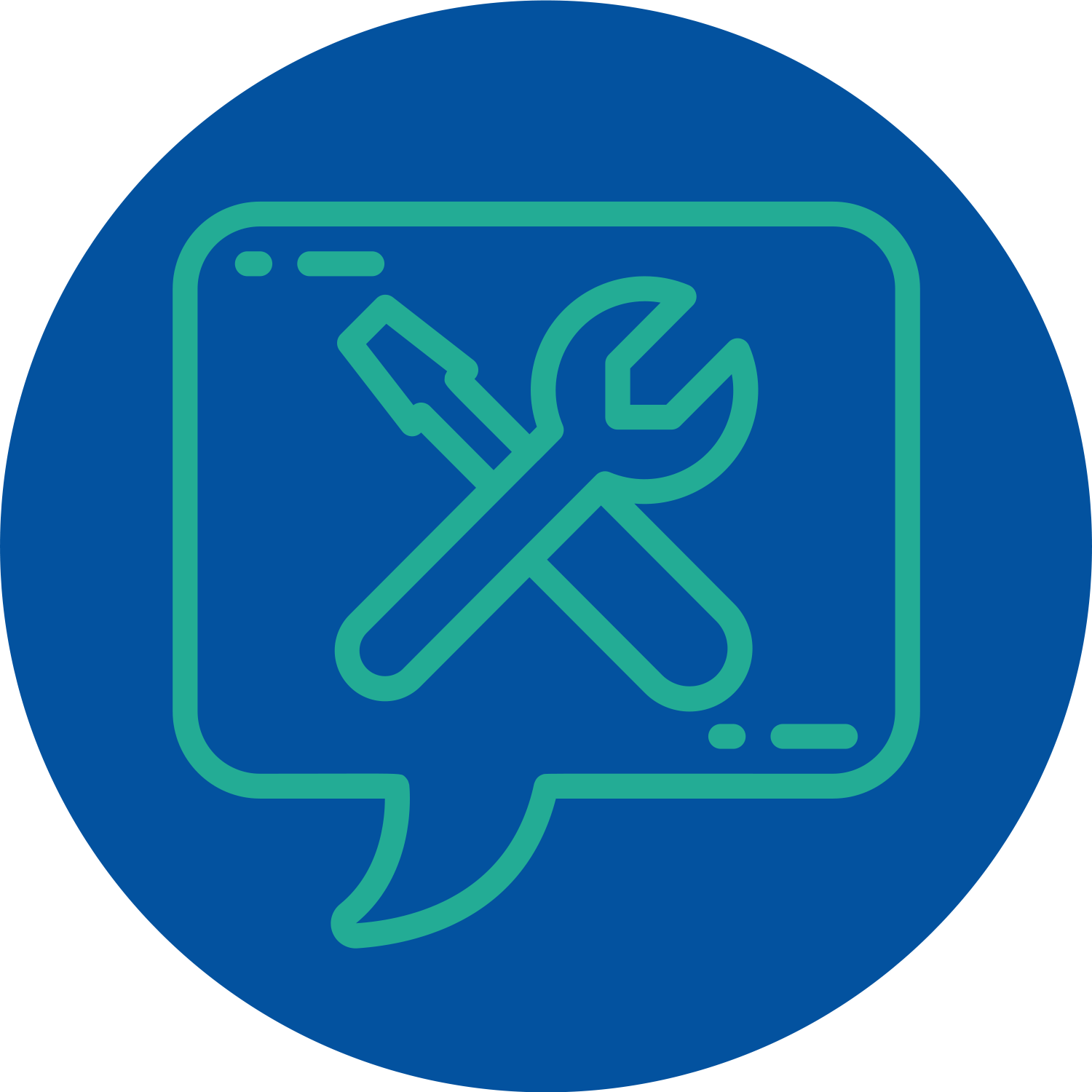
Track current and future service request
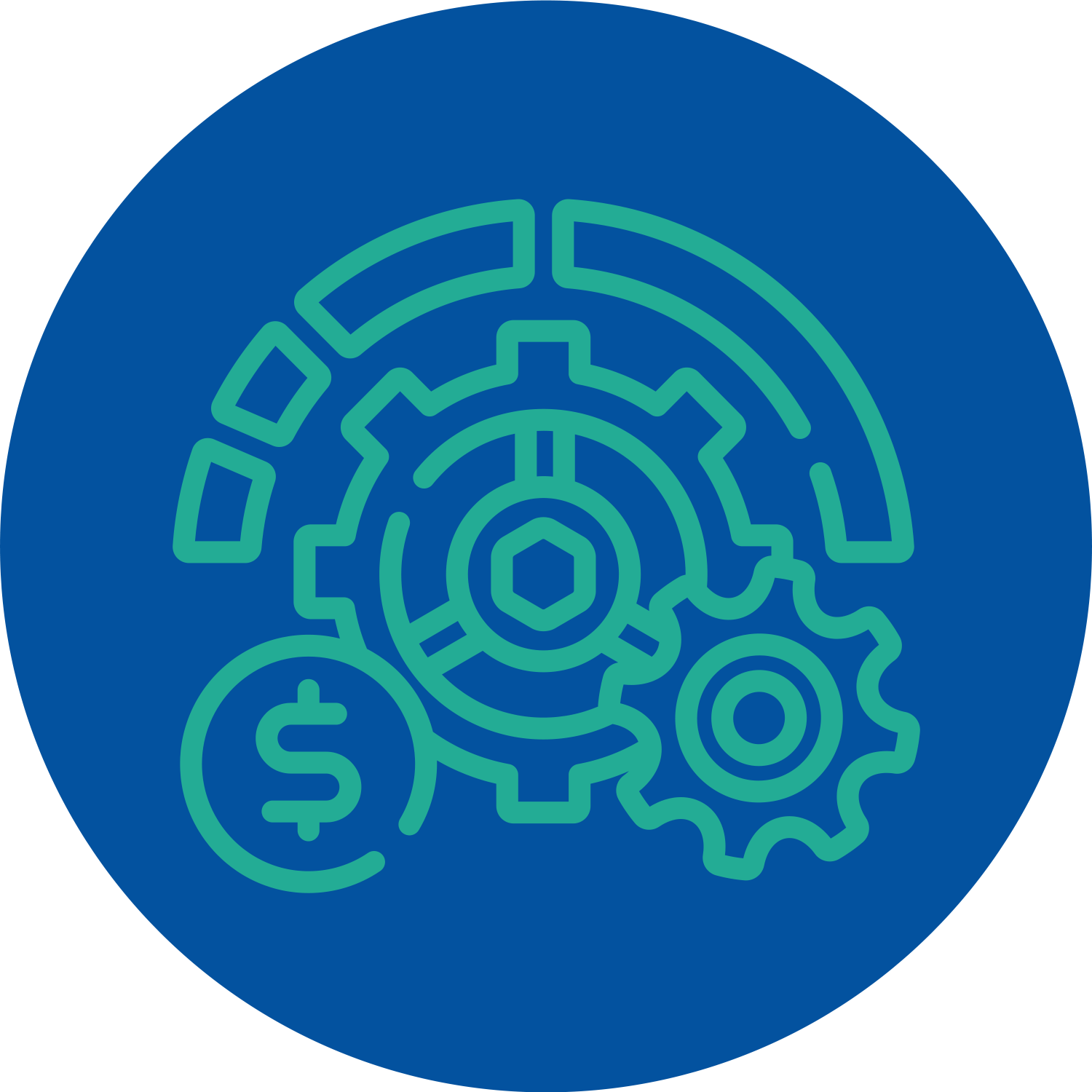
Eliminate costly inefficiencies related to preventable downtime or facility disruption
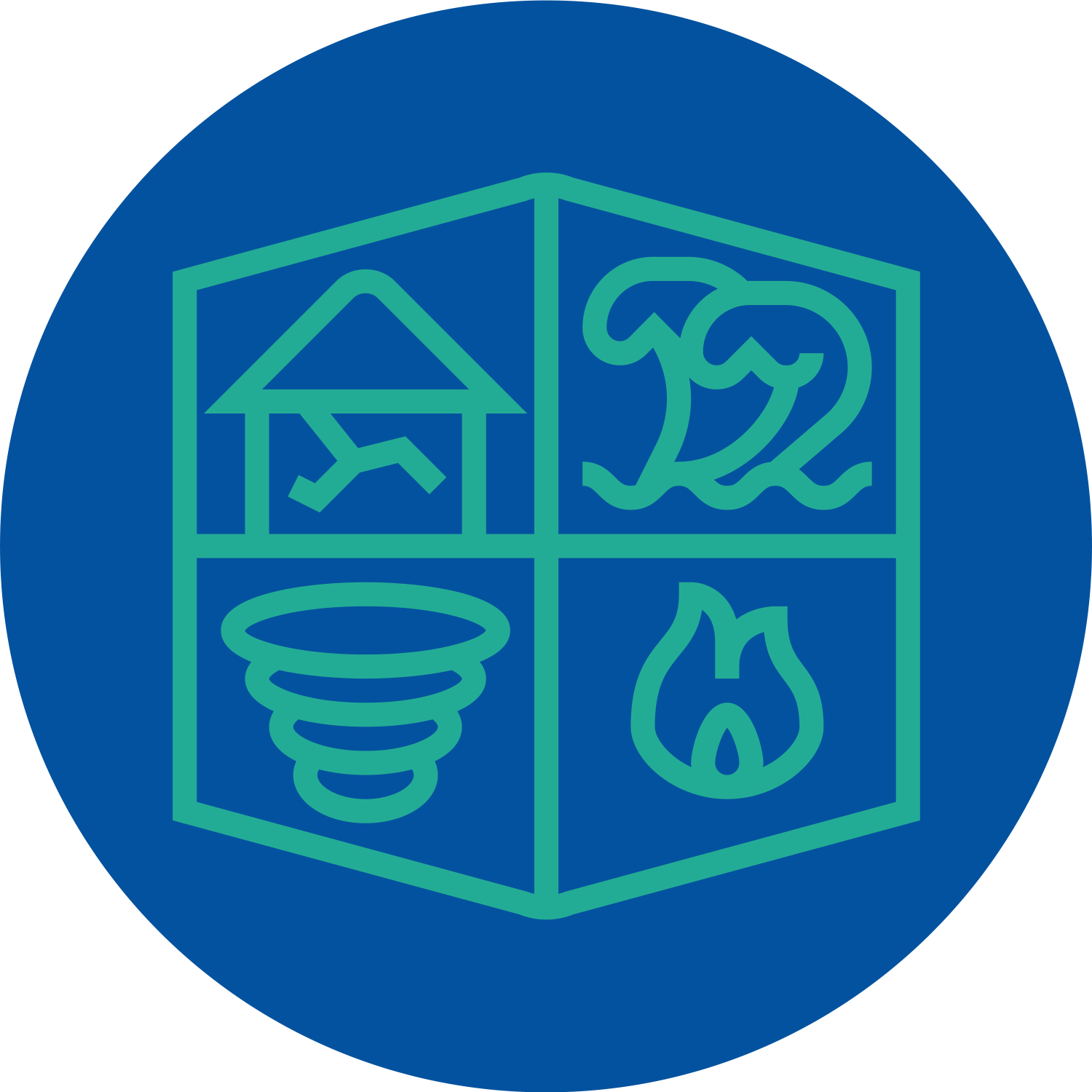
Plan for emergencies or natural disasters
Create a system for reporting problems
Building maintenance is often taken for granted because it entails behind-the-scenes work. People expect that the building will be kept clean, snow removed, trash removed, and AC will be functioning during the summer, but all of that takes work and planning.
A property maintenance management system automatically schedules planned maintenance tasks so nothing falls through the cracks. Building management scheduling software helps businesses better respond to emergencies by automatically triaging ongoing tasks, finding available technicians, and making it easy to locate necessary tools and parts.
Who uses building maintenance software?
Organizations that use building maintenance software programs include businesses that have physical facilities/offices, residential complexes, and government agencies.
Remember, building maintenance doesn’t only apply to office buildings or apartment units. Schools, manufacturing facilities, hospitals, and airports all have physical premises that require maintenance.
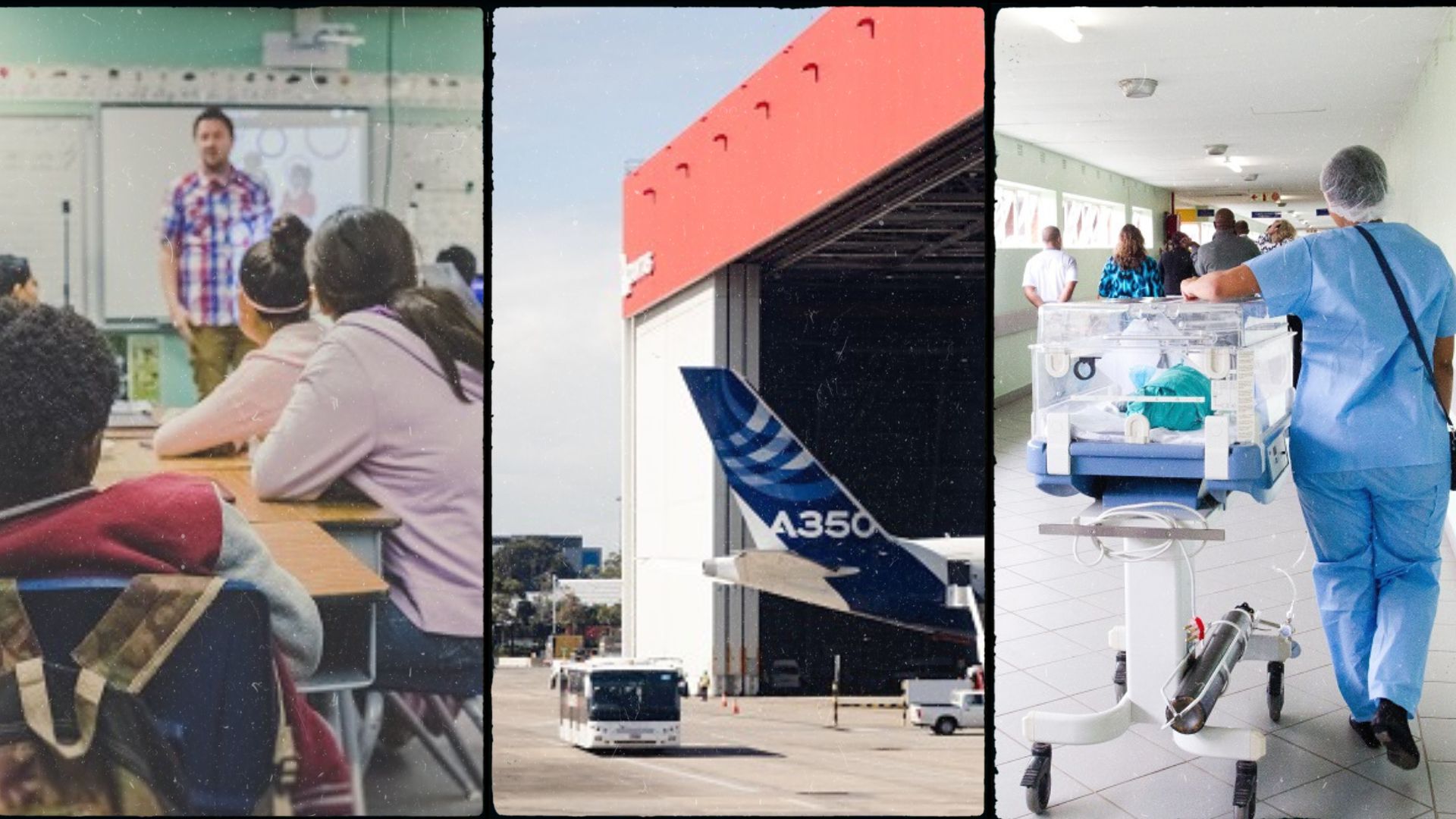
Key features of building maintenance software
Work order management
No more receiving work requests via phone, sticky notes, whiteboard, or word of mouth. Using a work order request system through your website creates a digital trail and reduces time spent on data entry. What’s more, building maintenance work order software automates the work request process for preventive and routine maintenance. Employees can log work order requests, set up preventive maintenance triggers, or connect to IoT sensors that generate work orders based on the real-time condition of an asset.
Lower maintenance costs
By keeping assets in good working condition, your organization can vastly reduce failure costs, which include the costs of corrective maintenance and associated risks to the safety of employees and/or tenants.
Increase the lifespan of your equipment
Asset management is the process of tracking and optimizing equipment lifecycle. An asset refers to any piece of equipment that is integral to the building’s safety and functionality. Proper asset management decreases administrative costs, improves service, and gives your organization visibility into asset utilization, costs, and maintenance. A CMMS allows you to streamline all asset information, including maintenance history, OEM recommendations, work orders, and everything in between.
Schedule preventive maintenance
Well-planned maintenance schedules waste less time, resources, and money. You can anticipate every element of maintenance like asset needs, production schedules, and inventory. As you gather more data over time, you can fine-tune the frequency of preventive maintenance tasks and ensure maintenance schedules use staff resources as effectively as possible.
Work order management with building maintenance software
Processing work orders in a timely manner is imperative to keeping up with building maintenance programs. While this sounds simple enough, the process of managing work orders consists of numerous steps, from creating work orders, prioritizing and assigning them to available technicians, and seeing them through to completion. More importantly, executing work orders requires the coordination of maintenance resources such as labor, assets, budgets, and parts.
When it comes to building maintenance, a work order management system enables your tenants to request work orders through an online portal.
BOX: What is a work order?
A work order is a request for a maintenance service to be performed. One-off requests come from stakeholders both within and outside the organization, such as an apartment tenant asking for a leaky faucet to be repaired. Alternatively, work orders can be recurring scheduled jobs set by the maintenance team to maintain equipment grounds, buildings, or vehicles.
Typically, the requester must fill out a digital form to initiate the work order request for building maintenance. The form serves as the primary form of communication and documentation for maintenance tasks.
Each work order request should contain the following information:
- Requester’s name and contact information
- Date of request
- Deadline (if applicable)
- Urgency level
- Ideal days of the week/times of day to perform maintenance
- Location of the asset
- Specifications of the asset (eg: serial number or barcode)
- Description of maintenance being requested
Work order management is also crucial for keeping track of recurring maintenance tasks such as inspections, corrective maintenance tasks, preventive maintenance, and emergency maintenance.
How a CMMS can help with building maintenance management
1. Track when, how, and why assets fail
In addition to the physical building itself, commercial and residential buildings come with a range of associated assets, from high-value assets like electrical and plumbing systems to relatively inexpensive items like lightbulbs and window treatments. Some assets will need more maintenance than others. Once you’ve collected enough data to make realistic predictions of when assets will fail, transfer their most high-value assets to a preventive maintenance plan.
However, you may elect to keep certain noncritical assets on a breakdown maintenance plan (consciously allowing an asset to run to failure) for budgetary reasons. With a CMMS, you can monitor historical asset failure, order parts ahead of time, and create RTF triggers so a work order is immediately issued to the relevant technician as soon as an asset fails. Finally, data reporting helps you anticipate when an asset will fail, how much it costs to maintain an asset, and more.
2. Optimize the workflow
Create a set of standard maintenance procedures technicians can follow for planned and unplanned building maintenance. CMMS features facilitate this process by providing quick access to maintenance logs for every asset, a spare parts management system that controls inventory so you never run out of replacement parts, and centralized information about each asset (OEM recommendations, fault patterns, and maintenance procedures).
3. Measure the effectiveness of your maintenance strategy
How much does your organization spend on building maintenance each fiscal year? A CMMS enables you to document how much downtime costs your organization, what causes it, and measure its impact on the bottom line. With data insights, you can determine whether or not breakdown maintenance is paying off, or if you need to put certain assets on a preventive maintenance plan.
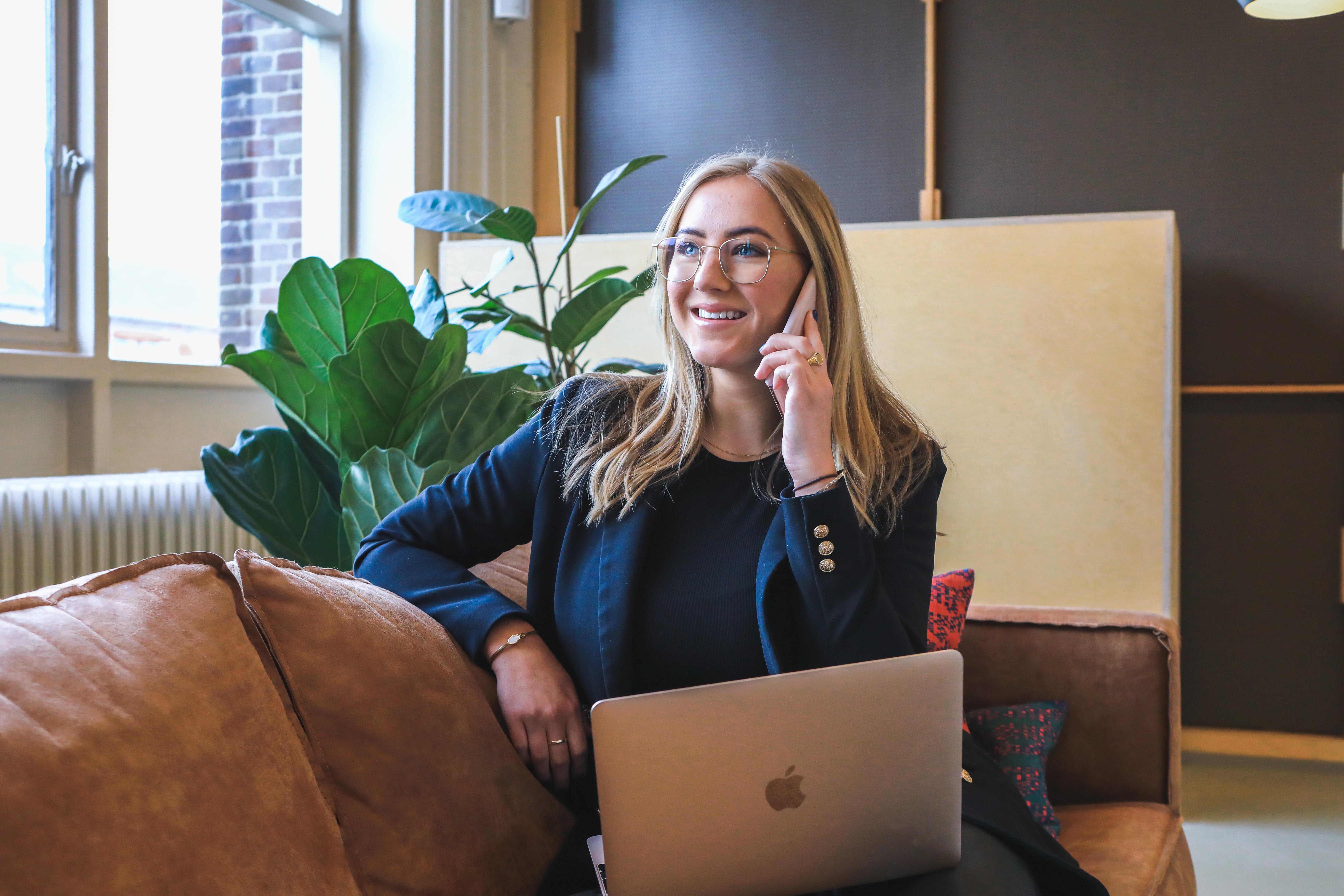